
BUILT TO GO THE DISTANCE
View Video
THE POWER OF VACUUM INFUSED RESIN CONSTRUCTION
Release Boatworks’ innovative manufacturing system utilizes the state-of-the-art Vacuum Infused Resin (VIR) molding process. Only a few manufacturers are using this highly sophisticated “closed-molded” process. VIR delivers a stronger, lighter, and more consistent product which is key when constructing sportfish boats that are designed to go far and fish hard. By pulling resin through the laminate under vacuum pressure, we achieve precise resin-to-glass ratios and eliminate excess weight without sacrificing structural integrity. The result is a stiffer hull, improved performance, better fuel efficiency, and a quieter ride offshore. It also means stronger and lighter parts, less waste and an environmentally friendly boatbuilding system.
The VIR process is not related to what is commonly known as “vacuum bagging,” a process used by many builders. Our boats are 100-percent composite, not wood, using only the finest materials. Vinylester resins, Kevlar, carbon, biaxial and triaxial woven fiberglass cloth and composite cores are used throughout the hull areas. Our stringers are foam-filled and fully encapsulated with fiberglass laminates and reinforced with a carbon composite layer for additional strength. The stringer grid system stiffens and provides the right amount of rigidity to the hull, while adding a gel coat finish below deck. With the composite cross-linked structural foams available today, every Release is lighter, stronger and stiffer than any competitor. The weight savings of the cored hull also equates to better fuel economy. Our boats still have the positive characteristics of the custom wooden classics, yet with the positive attributes listed above and also the advantages of no rot or insect problems.
01. The Right Materials
WHY VINYLESTER RESIN MATTERS
Release Boatworks’ focus on performance and strength dictates that we employ Vinylester resin. Simply put, it offers superior strength, flexibility, and resistance to water intrusion compared to traditional polyester resin and forms a tighter molecular bond, reducing the risk of blistering and improving overall durability—especially critical in our high-performance hulls.
This added resilience means better structural integrity under stress and longer-lasting finishes. While it’s certainly more expensive than polyester, it’s worth every dollar for those who demand serious offshore performance and longevity. At Release, compromise isn’t part of the build plan.
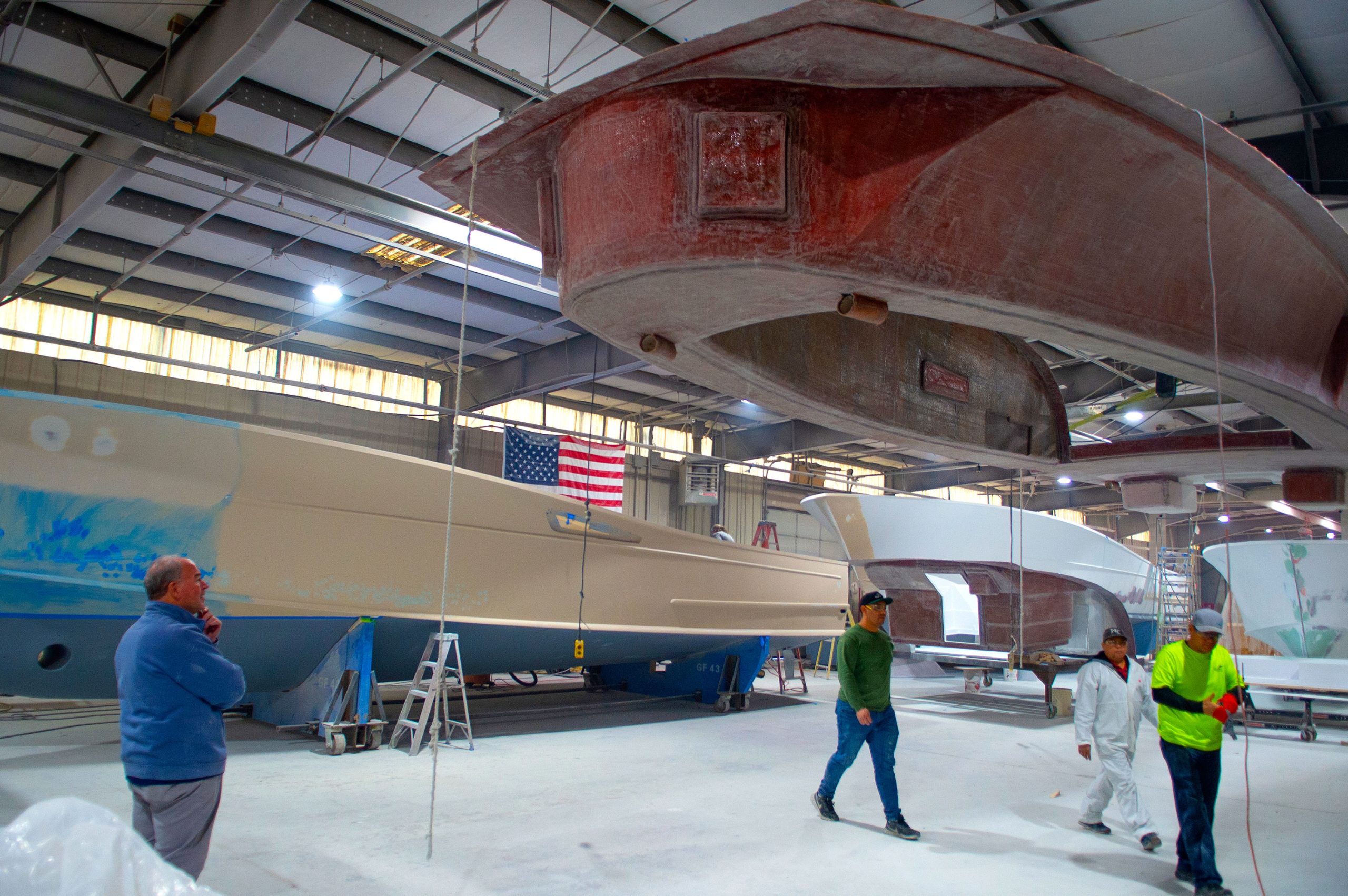
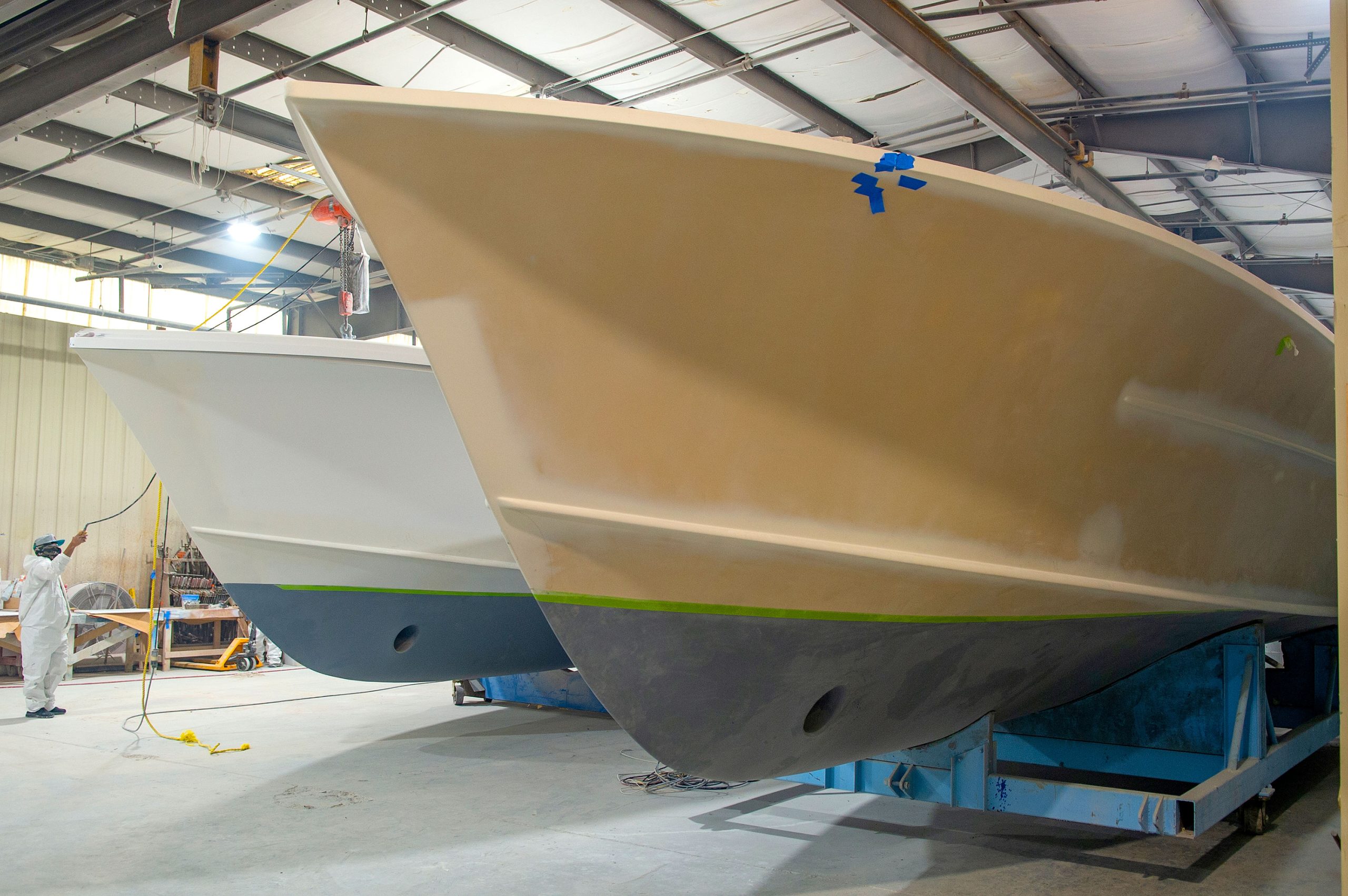
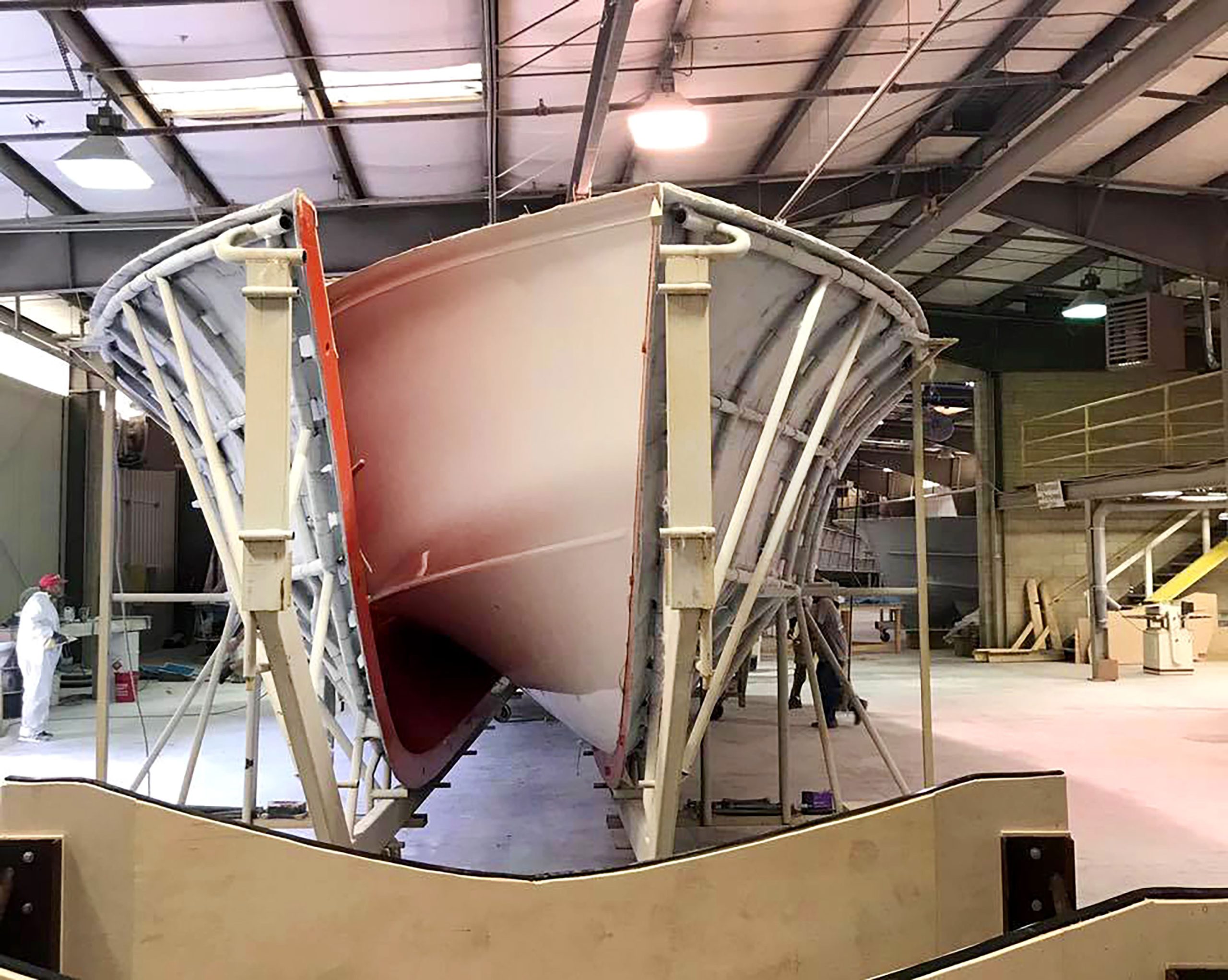
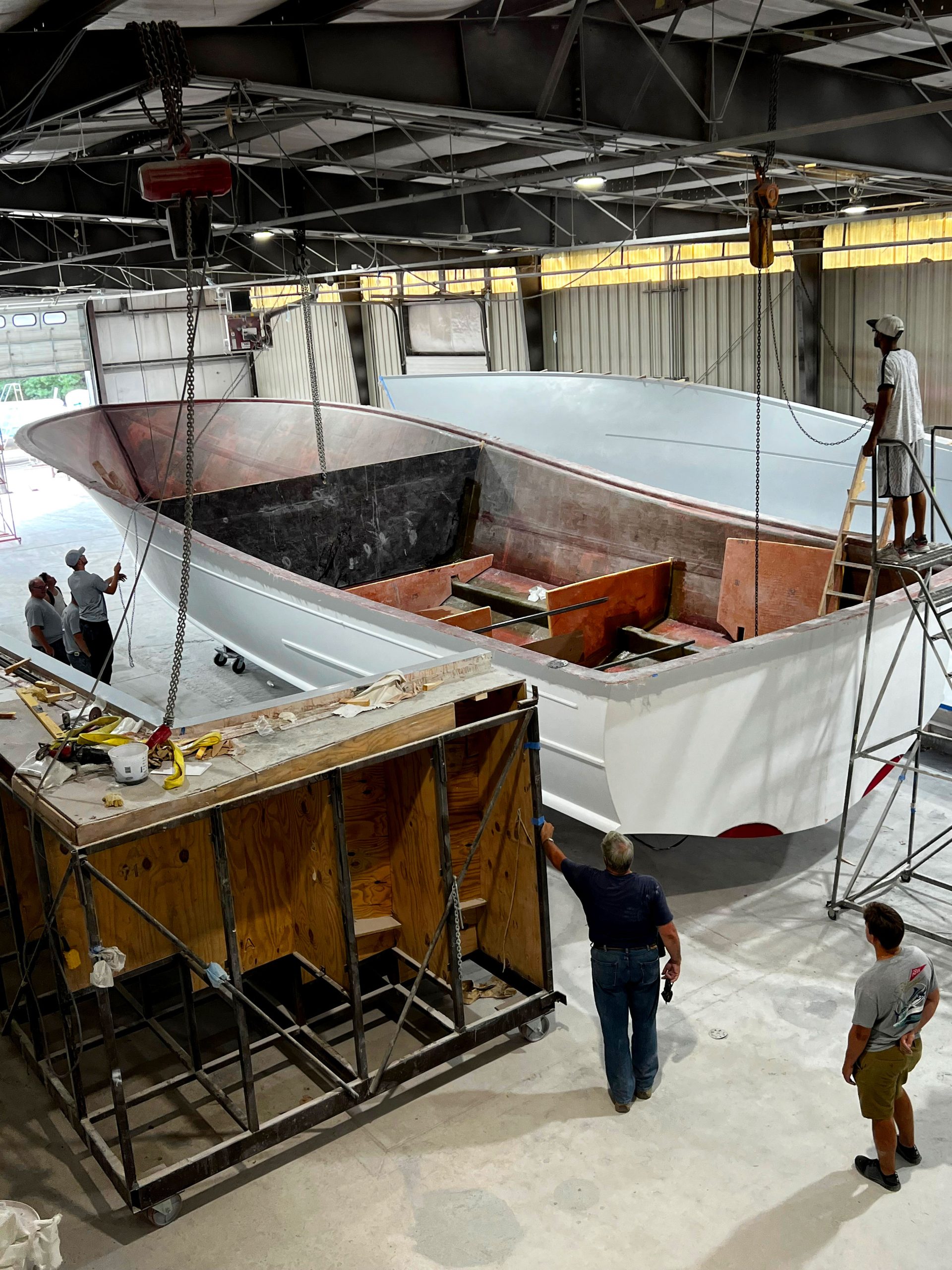
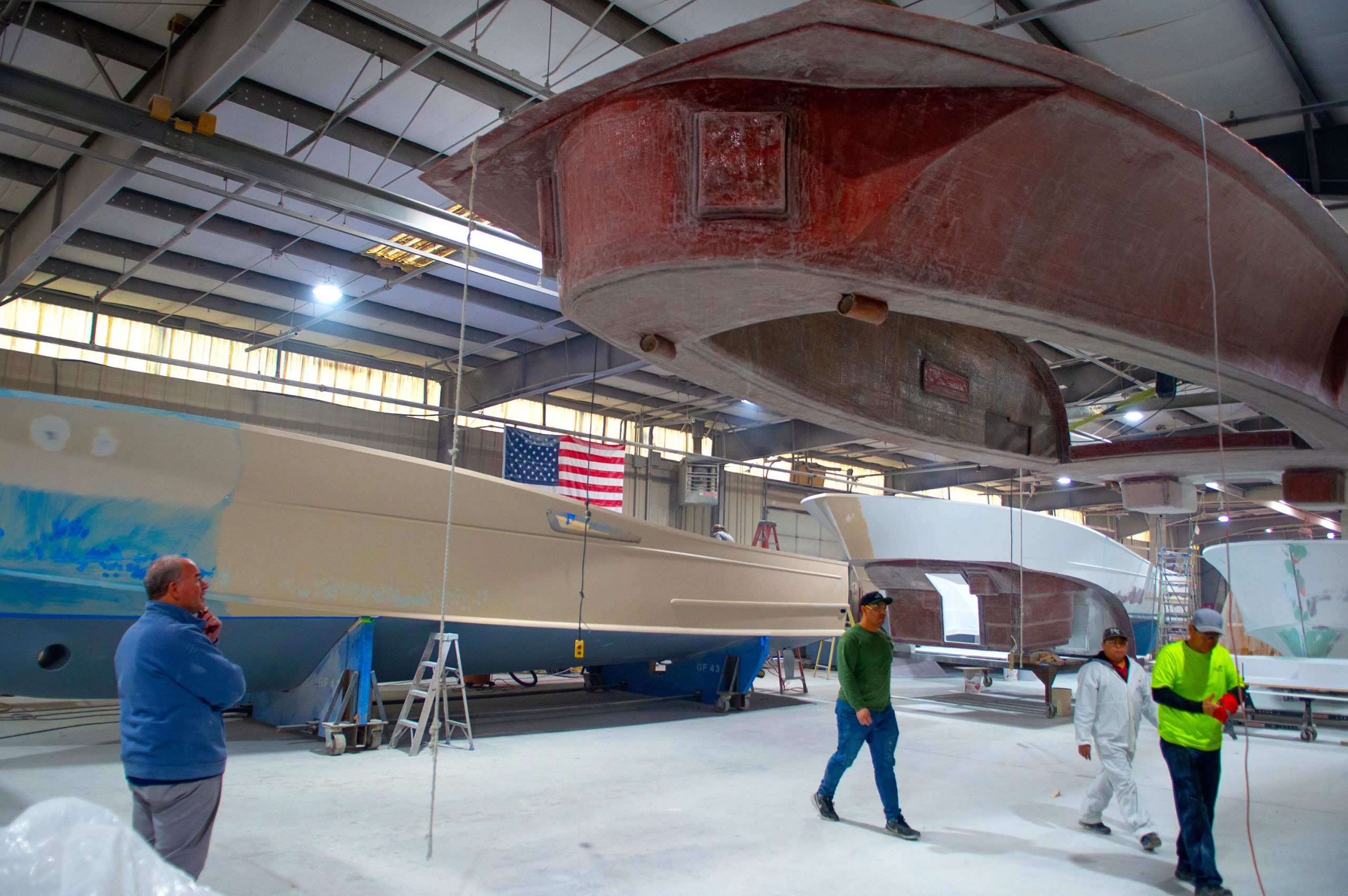
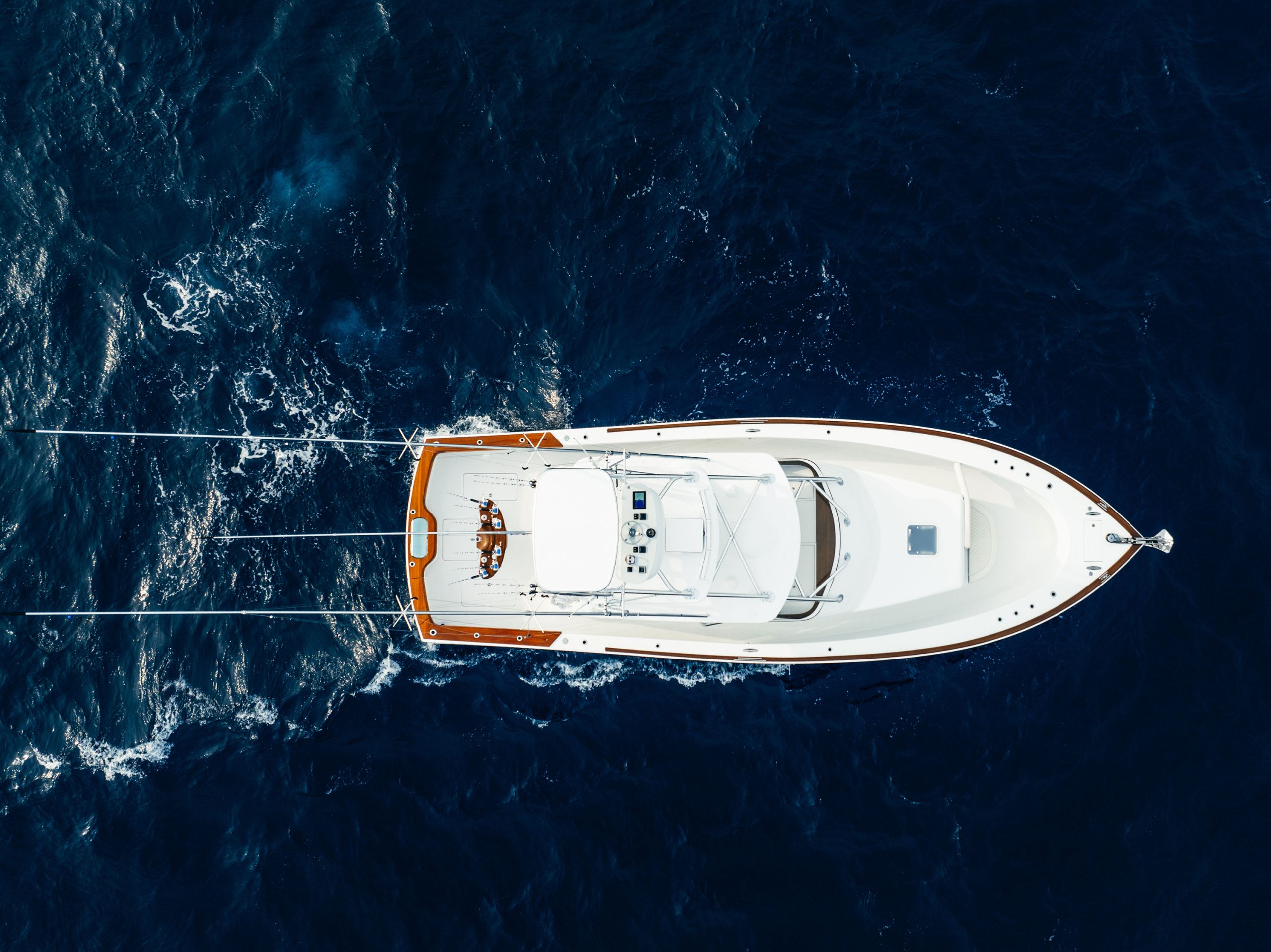
02. Built for the venture
FOAM-ENCAPSULATED STRENGTH. LIGHTWEIGHT PERFORMANCE.
Our foam-encapsulated stringer system delivers exceptional structural integrity without the added weight of traditional materials. We use high-density foam cores glassed into place to form a rigid, unified backbone that resists flex and absorbs vibration. The result is a stronger, quieter ride with less overall weight—meaning better fuel efficiency and performance offshore. Unlike wood-cored systems, foam won’t rot, absorb water, or degrade over time. It’s simply a smarter, more modern approach to boatbuilding.
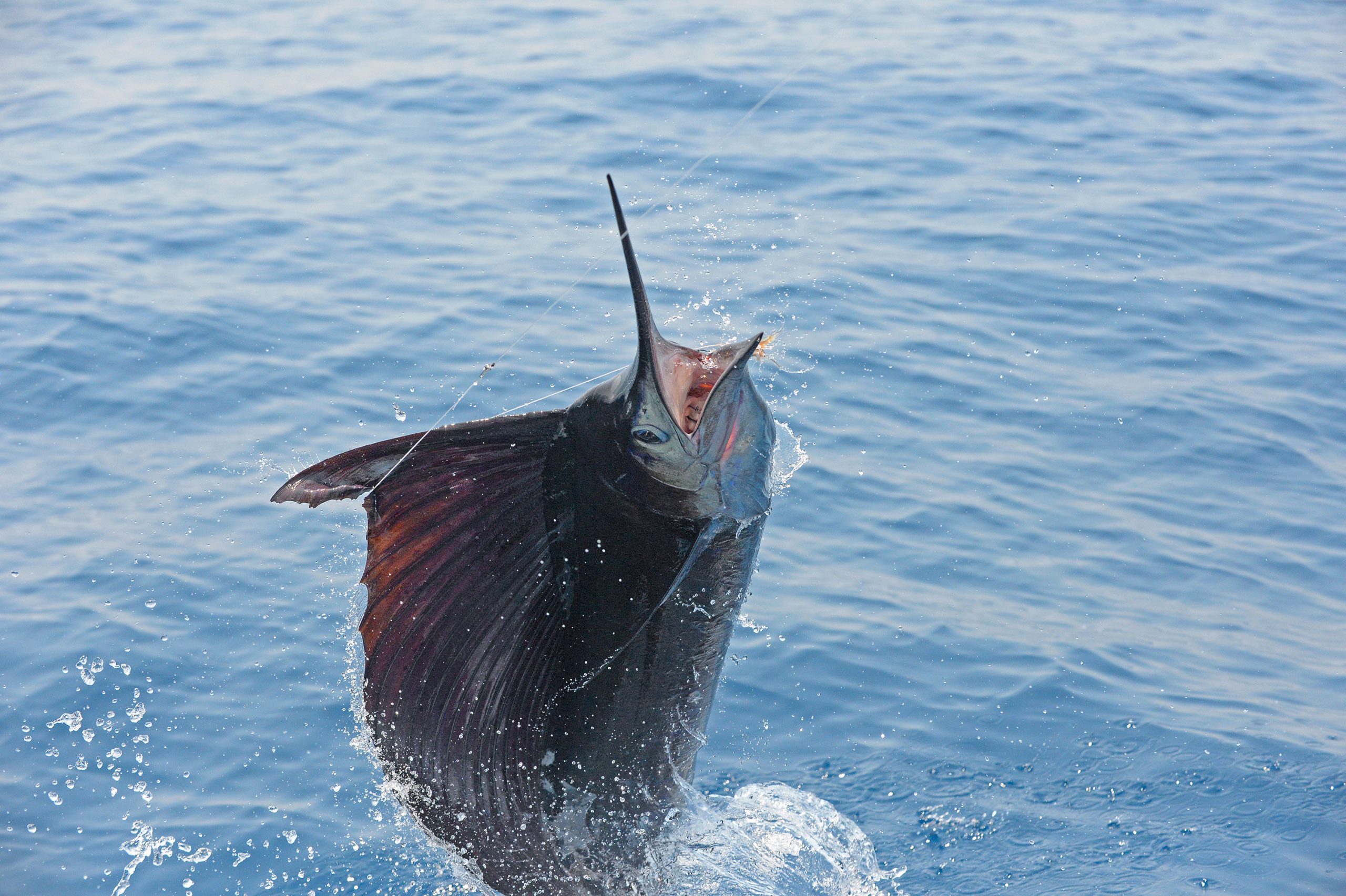